Rollon - Hardness Solutions In Linear Motion Rails
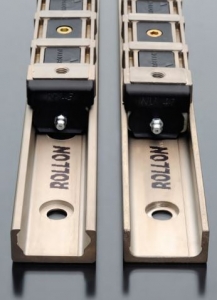
Rollon - Hardness Solutions In Linear Motion Rails
When it comes to linear motion rails, a high hardness value is critical. Unfortunately, some rail manufacturing processes don’t impart sufficient hardness to the rails. If hardness doesn’t extend to a sufficient depth, the component won’t be able to withstand heavy loads, resulting in time-consuming and costly downtime.
To gain maximum life for your linear guide, you’ll want to consider the hardening process, the material being hardened and how to finish the rail to optimize its performance. That way, quality manufacturers can make the best linear rail for your industrial application.
Consider induction hardening:
To harden their rails, a manufacturer can use nitriding, a heat treating process that creates a case-hardened surface with thicknesses between 0.2 and 0.3 mm. When you consider the kinds of heavy loads that are applied to industrial raceways, rails that have thin nitrided surfaces will tend to crack under load.
Induction hardening, on the other hand, creates a zone around the raceway with depths up to 5 mm. Compared to gas furnace heating and other conventional heat treatments, the process offers several advantages, including fast heating rates, low energy consumption and cost savings. Rails will also operate under heavy loads with no damage to the raceways over the course of their lifetime.
Use high-quality steel:
To achieve hardness levels that can stand up to the daily grind of industrial applications, high-quality linear motion rails need to be made from precise composition steel with a high carbon content. Induction hardening works by bringing out the natural properties of the metal, including its yield strength, malleability and toughness––which in turn increases the bearing’s strength and durability under variable loading conditions.
Rail Finish:
Once a raceway undergoes induction hardening, its surface can be further machined to improve its anti-friction capabilities. Grinding also makes hardened raceways more precise. If two raceways aren’t parallel, then their running quality is affected.
By contrast, grinding cannot be performed on raceways that undergo nitriding and other similar processes. Because the resulting case-hardened surface is so thin, grinding would remove the hard coating entirely.